Why Walnut Shells Work For Plastic Injection Molding
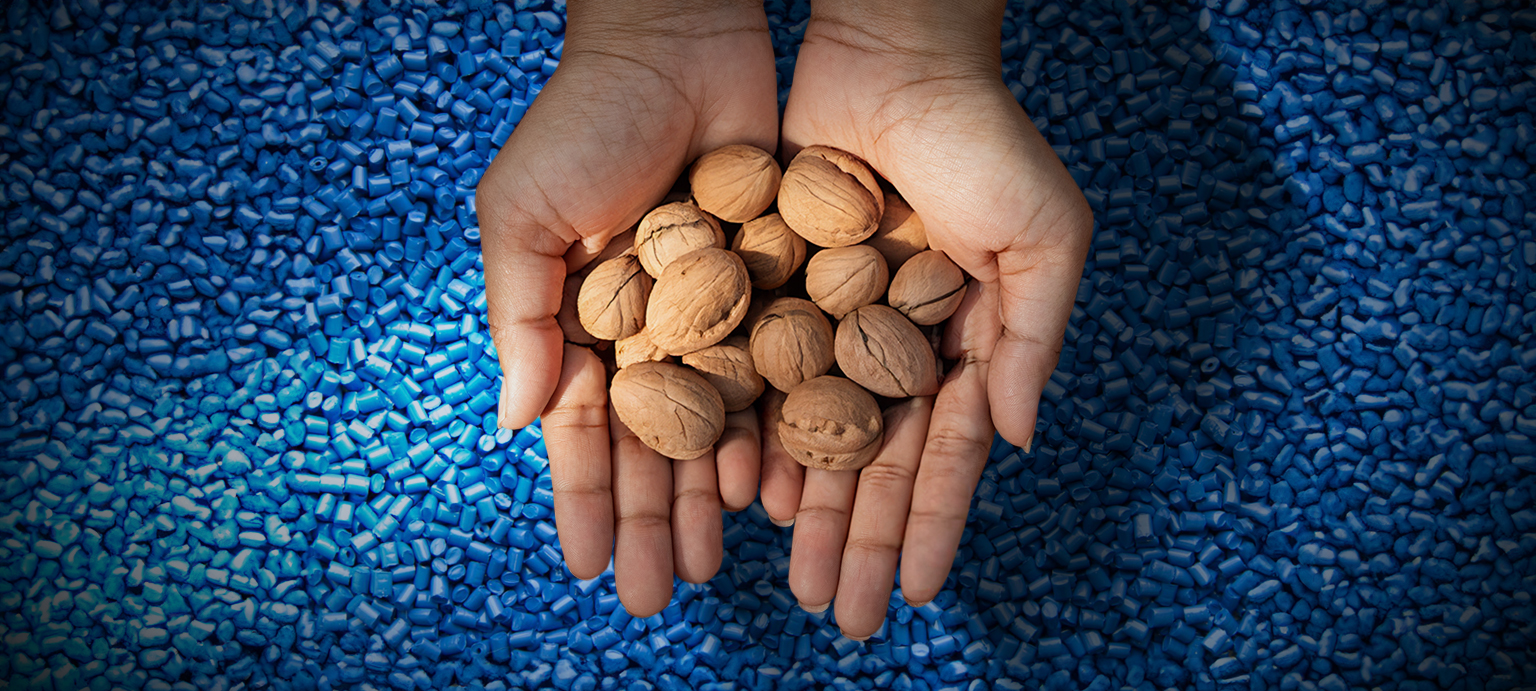
Calcium carbonite. Nylon. Walnut shells. When it comes to common fillers used in plastic injection molding, one of these things is definitely not like the others — and that’s a good thing. Read on to learn why walnut shells make an ideal filler material in plastic injection molding.
Affordable, cost-cutting material
Want to save money on fillers? Consider switching to walnut shells. This natural byproduct is frequently less expensive than other materials such as resin, crystalline plastics, polyethylene, and thermoplastic rubber. When ground down into a fine powder, walnut shells could also be used to replace a portion of pricier materials, giving your products the best of both worlds.
Protected from supply chain bottlenecks
The longer you have to wait for materials, the more your projects could get sidelined. Enter walnut shells. Eco-Shell plants thousands of walnut trees every year on our California farms, then supplies a variety of industries, including the molded plastics industry, with this versatile material thanks to our in-house raw material stock. Since walnut shells are annually renewable, they won’t get stuck in a supply chain bottleneck. Instead, they’ll be readily available for your products, which will keep your projects moving.
Enhanced durability
Your products are only as good as their materials. Thanks to their natural properties, walnut shells bring durability to the products they help fill. The lightweight material provides natural thermal insulation, which helps stabilize products. It also makes them more flexible and impact-resistant — which is great news for your bottom line.
Positive environmental impact
Consumers are steadily zeroing in on sustainability. A switch to walnut shells could make a difference — both economically and environmentally. Free of toxins and heavy metals, walnut shells are also all-natural, sustainable, and produced from a renewable source. Adding these to your products could increase consumer demand for goods manufactured with eco-friendly materials and environmentally sound practices.
Customized to fit your process
No matter your project, Eco-Shell can create custom grades to fit it. From 6/10 to 60/200 and an array of sizes in between, our grades are processed to address a variety of needs for the molded plastics industry. In fact, we regularly work with our partners to supply sample products for research and development. If you’re ready to see what walnut shells could do for you, contact us for a free sample kit.