How Walnut Shells Serve the Plastics Industry
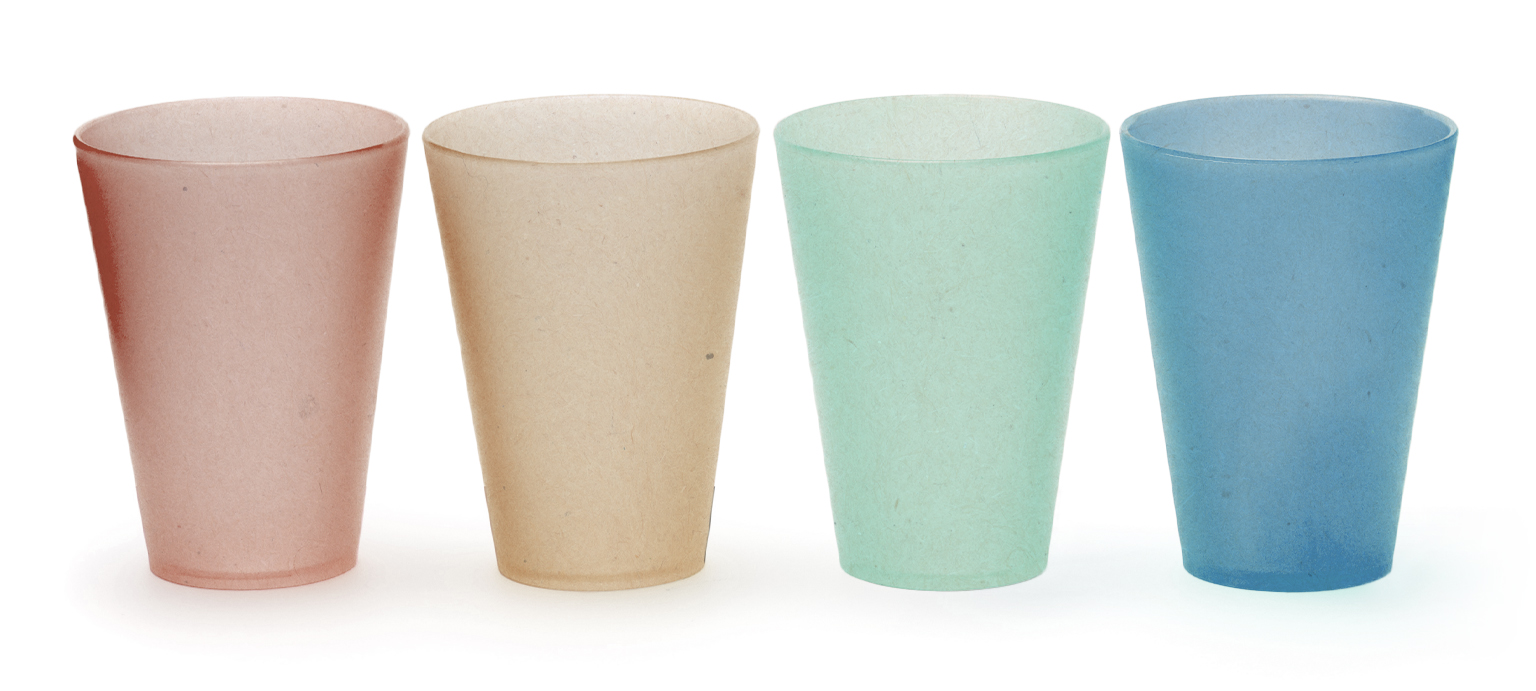
When it comes to the plastics industry, walnut shells may not be top of mind. But thanks to their abrasive and natural properties, this renewable ingredient serves multiple purposes throughout the industry. Learn more about how walnut shells bolster everything from blasting and polishing to filler material in certain plastic products.
Filler material that helps cut material costs
Looking for a cost-effective filler material? Need it to increase the strength of the plastic products while reducing shrinkage? Look no further than walnut shells. When ground into a powder and used as a filler, walnut shells can reduce overall costs by replacing a portion of pricier polymer materials. Plus, since they’re a renewable source, they’re readily available. They can also improve the mechanical properties of plastics, making them more flexible, stable, and impact resistant.
Reducing weight and strengthening reinforcement
Compared to more traditional fillers, walnut shells are relatively lightweight. This bodes well for applications where weight is critical, such as automotive and aerospace products. Adding walnut shells to these applications can help reduce the overall weight of the products, which could make a vital difference in performance.
Walnut shells are also a durable alternative to glass and carbon fibers and can be utilized as a natural reinforcement in plastics. Thanks to their natural properties, they can help improve the strength and rigidity of plastic components, particularly those requiring high structural integrity. What’s more, they can provide natural thermal insulation for applications where temperature control is crucial.
Surface finishing without damaging underlying plastic
If you’re cleaning and polishing plastic parts or molds, you want an abrasive that’s going to remove paint and rust. But that abrasive needs to be mild enough that it doesn’t damage the plastic that lies underneath the imperfections. Enter walnut shells. When crushed, they can be used in media blasting by cleaning, stripping, and preparing the surface safely and effectively.
The same principle can be applied to deburring and deflashing, or removing the excess materials at the edges or seams in plastics manufacturing. When used in tumbling, walnut shells can gently remove excess materials, improving both the surface quality and the aesthetics of the plastic components.
Sustainable alternative to traditional abrasives
Unlike sand and glass beads, walnut shells don’t produce harmful dust or fumes when utilized for applications such as blasting, polishing, and deburring. And their green credentials don’t stop there. A biodegradable ingredient, they serve as a sustainable alternative to synthetic fillers. And since they’re produced from a renewable source, their environmental impact is much lower than traditional abrasives.
Utilizing walnut shells in the plastics industry can appeal to a wide array of producers looking for eco-friendly ways to reduce their impact on the planet. And that’s a win for everyone.